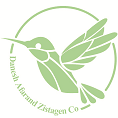
@2025 Afarand., IRAN
ISSN: 2008-2630 Iranian Journal of War & Public Health 2016;8(2):119-125
ISSN: 2008-2630 Iranian Journal of War & Public Health 2016;8(2):119-125
Effect of Silicone Brim Socket of Transfemoral Prosthesis on Pressure Level in Proximal Weight Bearing Areas and Comparing with Conventional Socket
ARTICLE INFO
Article Type
Case ReportAuthors
Ejraei Dolat Abad H. (*)Haji Aghaei B. (1)
Jalali M. (1)
Saeedi H. (1)
(*) Orthotics & Prosthetics Department, Rehabilitation Faculty, Iran University of Medical Sciences, Tehran, Iran
(1) Orthotics & Prosthetics Department, Rehabilitation Faculty, Iran University of Medical Sciences, Tehran, Iran
Correspondence
Address: Orthotics & Prosthetics Department, School of Rehabilitation, Madad Karan Street, Shah Nazari Street, Mother Square, Tehran, IranPhone: +982122220947
Fax: -
habib.ejraei70@gmail.com
Article History
Received: February 23, 2016Accepted: April 20, 2016
ePublished: June 18, 2016
BRIEF TEXT
… [1-3].Comfort of socket has an important role on the performance and the use of prosthesis [4, 5].
… [6-14]. Studies show that most skin problems are usually caused by pressure on upper weight-bearing areas in the socket. In these areas, the pressure on the stump is twice as much as other socket`s areas [15].
The purpose of this study was designing and constructing trans-femoral prosthesis modified silicone edge socket and investigating its effect on the pressure in the region of upper weight bearing compared to conventional socket without the silicon edge.
This study is a case study with a single sample.
A 38-year-old man with a traumatic amputation of the right femoral trance with a stump with length of 28 cm was evaluated.
Inclusion criteria included traumatic amputation, placing the length of stump in the middle third of the femur, normal body weight index (18.5 to 25 kg/per square meter), and age range of 25 to 55 years; and exclusion criteria included orthopedic problems, disrupting gate limb, balance problems, severe volume changes in the stump, existence of contracture flexion more than 20 degree in the stump, severe weakness in muscle stump and the existence of extensive scar tissues.
Two sockets were made for this person, one with conventional method and another one with silicon edge. Also, for measuring pressure by using FSR (Force Sensitive Register) and Arduino Due microcontroller board, pressure measurement device was built. Construction of pressure measurement device: FSR (Inter Link, USA) was used as the receiver of pressures for making the pressure measurement device. By creating relationship between applied force and decrease in the resistance, amount of force applied to FSR can be measured. Of the 10 FSR used in the construction of this device, 8 of them were placed into the socket in the parts of adductor longus tendon, on the inferior public Ramos, above scarpa triangle, femoral trochanter, the outer part of ischium, the place of rectus femoris muscle, and 2 sensors in the ischium. Information received by the FSRs were entered Arduino Due microcontroller board used in making the machine and it was processed according to its programming and it was stored in the memory card installed on the device. Two other sensors were placed under the amputee`s prosthetic leg in the heel and metatarsal heads in order to recognize the times of the most pressures on the heel sensor and the most pressure on the metatarsal heads by using the information received from these two sensors. Building socket with silicon edge: After molding the stump, necessary amendments were carried out and final plaster mold was achieved. Then pouring of silicon in proximal section was performed. For making socket with silicon edge, medical grade silicon (Shore 35, COP Company, France) was used. After doing lamination, hard edges of the socket at the correct distance from the silicon was cut. Then, using the same positive mold, socket was developed according to the conventional method. Measuring of the pressure: the pressures were measured on the states of standing on two feet, standing on a prosthetic leg, and walking on a prosthetic leg at the time of maximum pressure on the heel sensor and the maximum pressure on the metatarsals` head. Loading and pulling response times was recognized according to the information obtained from the two sensors placed under the person`s prosthetic leg. Standing on two legs: First, the pressure measurement device sensors were put in the determined places. Then, the user of prosthetic socket put the socket and after walking in the period of time that he had selected (when the prosthesis socket was fully in place), he was asked to place one of his foot on the scale and another foot on the platform to compensate for the length difference, and he was asked to divide his weight equally on both legs. After ensuring that the scale shows the half of the person`s weight, by pressing the button, pressure measurement device began to received data, and after 2 seconds it started to receive information, and stored the obtained information on the memory card within 15 seconds. Standing on a prosthetic leg: in this case, the prosthetic user was asked to sit on the prosthetic leg while his body was on the portrait mode, stand on his prosthetic leg and put the hand on the opposite side of amputation at an angle of 90 degrees to the wall (in order to make balance). In this case, also, by turning on the device, the pressure between stump and socket was measured for 15 seconds. Pressure measurement in walking mode: In this mode, by setting up the device for measuring the pressures, the prosthesis user was asked to walk on a direct path with a length of 10 m and his own selected speed, and the information was stored on the memory card. After finishing the measurement in one of the sockets, after opening the screw, the first socket was removed from the prosthesis and the next socket was replaced; and the sensors were installed in the place similar to the previous socket. To maintain the similarity of two sockets, the alignment changes which had been made during turning the socket was removed while the prosthesis user was walking and the person was adopted to the new socket. After these actions, the measurements was repeated for the next socket. After the measurements, the data stored in the memory card transferred to computer. Using MATLAB software, diagrams related to each sensor in different conditions were drawn and based on the diagrams, the amount of force between the stump and socket was extracted.
Standing position on two feet: Maximum pressure received at the person standing on two legs, were in the socket with silicon edge and in the conventional socket in sensor no. 8. The least amount of pressure on both sockets were on the sensor no. 4 and it was equal to zero. On the standing position on two feel, in all sensors except sensor no. 8 the pressures on the socket with silicon edge was reduced in the silicon edge socket compared to the conventional socket. However, in the sensor no. 8 in the socket with silicon edge, increase in pressure was observed. Walking in the response time loading mode: in this mode, the most received amount of pressure in both sockets was in sensor no. 8, and the minimum registered pressure in both sockets were in the sensor no. 4. In this case no pressure was received in the sensor no. 4 in the conventional socket, but in the same sensor in the socket with silicon edge the pressure equal to 0.23 kPa was recorded. Also, in the sensor no. 7, also, the increase in pressure was observed but in the other sensors, the pressure was decreased. Walking mode while pushing off: the highest received pressure in this case was in the conventional socket and the silicon edge socket in the sensor no. 8. The least amount of received pressure was in the conventional and silicon edge sockets in the sensor no. 4. In this case, the amount of pressure in the sensors no. 7 and 8 in the both sockets were the same. This is while other sensors in the silicon edge socket showed less pressure compared to conventional socket in this state (Table 1).
Studies show that the maximum amount of pressure between stump and socket in a trans-femoral amputee are in the upper weight-bearing areas of the socket.
It is suggested that future studies pressure on more people and more walking modes be studied. Also, it is suggested that pressures be measured in all internal levels of socket.
Of the limitations of this study were few number of samples, lack of measuring the pressure while walking and lack of measuring the pressure in all internal surfaces of the socket.
Using socket with silicon edge in trans-femoral prosthesis reduces the pressures on the stamp and more comfort of an amputee compared to the conventional socket.
Many thanks to Mr. Reze Akhavan, MA students of medical engineering at Islamic Azad University, Tehran North Branch, because of his sincere cooperation in the process of making a pressure measurement device used in this study.
Non-declared
This study was confirmed in the ethical committee of the university related to the authors.
This study was funded by the authors. … [16, 17].
TABLES and CHARTS
Show attach fileCITIATION LINKS
[1]Ziegler-Graham K, MacKenzie EJ, Ephraim PL, Travison TG, Brookmeyer R. Estimating the prevalence of limb loss in the United States: 2005 to 2050. Arch Phys Med Rehabil. 2008;89(3):422-9.
[2]Saeid Zakerin M, Hoviat Talab K, Shahabi M. The effect of home visit on self care of war-disabled people with lower limb amputation. Pajohandeh. 2000;5(1):107-11. [Persian]
[3]Klotz R, Colobert B, Botino M, Permentiers I. Influence of different types of sockets on the range of motion of the hip joint by the transfemoral amputee. Ann Phys Rehabil Med. 2011;54(7):399-410.
[4]Dumbleton T, Buis A, McFadyen A, McHugh BF, McKay G, Murray KD, et al. Dynamic interface pressure distributions of two transtibial prosthetic socket concepts. J Rehabil Res Dev. 2009;46(3):405-15.
[5]Klute GK, Kallfelz CF, Czerniecki JM. Mechanical properties of prosthetic limbs: adapting to the patient. J Rehabil Res Dev. 2001;38(3):299-307.
[6]Smith DG, Michael JW, Bowker JH, Surgeons AAoO. Atlas of amputations and limb deficiencies: surgical, prosthetic, and rehabilitation principles. IL: American Academy of Orthopaedic Surgeons Rosemont; 2004.
[7]Lusardi MM, Jorge M, Jorge M, Nielsen CC. Orthotics and prosthetics in rehabilitation. 3rd edition. United States: Elsevier Health Sciences; 2012.
[8]Klute GK, Rowe GI, Mamishev AV, Ledoux WR. The thermal conductivity of prosthetic sockets and liners. Prosthet Orthot Int. 2007;31(3):292-9.
[9]Lee WC, Zhang M, Mak AF. Regional differences in pain threshold and tolerance of the transtibial residual limb: Including the effects of age and interface material. Arch Phys Med Rehabil. 2005;86(4):641-9.
[10]Jia X, Zhang M, Lee WC. Load transfer mechanics between trans-tibial prosthetic socket and residual limb-dynamic effects. J Biomech. 2004;37(9):1371-7.
[11]Dudek NL, Marks MB, Marshall SC, Chardon JP. Dermatologic conditions associated with use of a lower-extremity prosthesis. Arch Phys Med Rehabil. 2005;86(4):659-63.
[12]Ali S, Osman NA, Mortaza N, Eshraghi A, Gholizadeh H, Wan Abas WA. Clinical investigation of the interface pressure in the trans-tibial socket with Dermo and Seal-In X5 liner during walking and their effect on patient satisfaction. Clin Biomech. 2012;27(9):943-8.
[13]Visscher MO, Robinson M, Fugit B, Rosenberg RJ, Hoath SB, Wickett RR. Amputee skin condition: occlusion, stratum corneum hydration and free amino acid levels. Arch Dermatol Res. 2011;303(2):117-24.
[14]Meulenbelt HE, Geertzen JH, Jonkman MF, Dijkstra PU. Skin problems of the stump in lower limb amputees: 1. A clinical study. Acta Derm Venereol. 2011;91(2):173-7.
[15]Neumann ES, Wong JS, Drollinger RL. Concepts of pressure in an ischial containment socket: Measurement. J Prostheti Orthot. 2005;17(1):2-11.
[16]FSR 402 Short [Internet]. Los Angeles: Interlink Electronics [Cited 2015, 5 November]. Available from: http://www.interlinkelectronics.com/FSR402.php
[17]Baars EC, Geertzen JH. Literature review of the possible advantages of silicon liner socket use in trans-tibial prostheses. Prosthet Orthot Int. 2005;29(1):27-37.
[2]Saeid Zakerin M, Hoviat Talab K, Shahabi M. The effect of home visit on self care of war-disabled people with lower limb amputation. Pajohandeh. 2000;5(1):107-11. [Persian]
[3]Klotz R, Colobert B, Botino M, Permentiers I. Influence of different types of sockets on the range of motion of the hip joint by the transfemoral amputee. Ann Phys Rehabil Med. 2011;54(7):399-410.
[4]Dumbleton T, Buis A, McFadyen A, McHugh BF, McKay G, Murray KD, et al. Dynamic interface pressure distributions of two transtibial prosthetic socket concepts. J Rehabil Res Dev. 2009;46(3):405-15.
[5]Klute GK, Kallfelz CF, Czerniecki JM. Mechanical properties of prosthetic limbs: adapting to the patient. J Rehabil Res Dev. 2001;38(3):299-307.
[6]Smith DG, Michael JW, Bowker JH, Surgeons AAoO. Atlas of amputations and limb deficiencies: surgical, prosthetic, and rehabilitation principles. IL: American Academy of Orthopaedic Surgeons Rosemont; 2004.
[7]Lusardi MM, Jorge M, Jorge M, Nielsen CC. Orthotics and prosthetics in rehabilitation. 3rd edition. United States: Elsevier Health Sciences; 2012.
[8]Klute GK, Rowe GI, Mamishev AV, Ledoux WR. The thermal conductivity of prosthetic sockets and liners. Prosthet Orthot Int. 2007;31(3):292-9.
[9]Lee WC, Zhang M, Mak AF. Regional differences in pain threshold and tolerance of the transtibial residual limb: Including the effects of age and interface material. Arch Phys Med Rehabil. 2005;86(4):641-9.
[10]Jia X, Zhang M, Lee WC. Load transfer mechanics between trans-tibial prosthetic socket and residual limb-dynamic effects. J Biomech. 2004;37(9):1371-7.
[11]Dudek NL, Marks MB, Marshall SC, Chardon JP. Dermatologic conditions associated with use of a lower-extremity prosthesis. Arch Phys Med Rehabil. 2005;86(4):659-63.
[12]Ali S, Osman NA, Mortaza N, Eshraghi A, Gholizadeh H, Wan Abas WA. Clinical investigation of the interface pressure in the trans-tibial socket with Dermo and Seal-In X5 liner during walking and their effect on patient satisfaction. Clin Biomech. 2012;27(9):943-8.
[13]Visscher MO, Robinson M, Fugit B, Rosenberg RJ, Hoath SB, Wickett RR. Amputee skin condition: occlusion, stratum corneum hydration and free amino acid levels. Arch Dermatol Res. 2011;303(2):117-24.
[14]Meulenbelt HE, Geertzen JH, Jonkman MF, Dijkstra PU. Skin problems of the stump in lower limb amputees: 1. A clinical study. Acta Derm Venereol. 2011;91(2):173-7.
[15]Neumann ES, Wong JS, Drollinger RL. Concepts of pressure in an ischial containment socket: Measurement. J Prostheti Orthot. 2005;17(1):2-11.
[16]FSR 402 Short [Internet]. Los Angeles: Interlink Electronics [Cited 2015, 5 November]. Available from: http://www.interlinkelectronics.com/FSR402.php
[17]Baars EC, Geertzen JH. Literature review of the possible advantages of silicon liner socket use in trans-tibial prostheses. Prosthet Orthot Int. 2005;29(1):27-37.